quality craftsmanship as standard
We provide a complete sculpture casting service for professional and amateur artists working on commission or private projects.
The foundry casts in silicon bronze and can accommodate projects from 1 to 1,000 kilos. In fact we relish a challenge and enjoy coming together as a team to work on difficult or demanding projects, however large or small, taking pride in fulfilling the artist’s brief, however unusual.
Talos Art Foundry casts bronze sculpture using the lost wax technique (cire perdue) method. Lost wax casting was first used by the Ancient Egyptians around 2500BC and the technique remains largely unchanged.
We also offer a complete sculpture installation service, and can assist with the restoration and repair of bronze sculptures which have been damaged through time, accident or vandalism.


GETTING STARTED
We are looking forward to working with you here at Talos and understand that it is not one approach that fits all. Works come in all shapes and sizes and can be at different stages along the casting process. We will work with you to realise your creative vision, whatever your start, or end point.
To get started we ask for images and dimensions of the piece and offer all artists (and their clients) to come with their sculpture to visit the foundry and see how we work. Together we can confirm your requirements and quote for the work. Once accepted the job will be add the work schedule.
We like to provide the complete casting process for our artists and the benefit of continuity is seen in the results. However we understand that is not always the required approach and provide a number of different start and end points - cost and timelines adapt accordingly.
-
Mould only
-
Mould to finishing (patina and mounting onto a base if used)
-
Wax to finishing (from an existing mould)
-
Wax to fettling
-
Running up to fettling from a wax or 3D print provided by the artist
-
Running up to finishing from a wax or 3D print provided by the artist
If you are not sure where to start or are concerned about how to turn you work into the finished sculpture we offer further consultancy to help advise and support.


MOULD MAKING
Our team have the capacity and experience to create moulds and wax models at any size* and help our artists to scale up or down from original works without loosing any of the original details. This is achieved by creating either simple blocks or complex multi-part moulds as required to meet the individual need of each project.
MOULDING MATERIALS
For most applications, we use a silicone rubber material to make the moulds with either plaster or Jesmonite as the 'jacket' (or case) to hold the rubber in place. These moulds enable us to make wax copies of the artists’ original sculpture, which are the key to the ‘lost wax’ casting technique.
In the instances where using silicone is impractical our mould makers have all the skills to make interlocking plaster piece moulds or traditional alginate moulds.
*Sculptures either too fragile or too large to transport can be moulded in the artist’s studio or on site by arrangement.


WAX MODELLING & BRONZE CASTING
We make a hollow wax (approx. 5mm thick) from the mould which is a reproduction of the original sculpture and using hot tools we ‘touch up’ the seam line and any imperfections on the surface of the wax. We then invite the artist in to inspect the wax and they can do some minor alterations at this stage.
We then ‘run up’ the wax which is essentially the first stage of making a mould for the molten bronze. Often the wax is kept in one piece if it is within our size limit, but if it is larger it will be cut into several pieces. The run up waxes are then dipped or ‘invested’ and sprinkled with a granular ceramic material for strength and allowed to dry thoroughly between each dip
To cast the shells they are placed in groups in the ‘de-waxer’ a large, adapted ceramic kiln. The heat from the de-waxer fires the shells and melts out the wax until you are left with a hollow shell for the metal which is why it is called the lost wax process.
We only cast using silicon bronze.

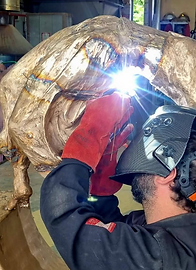
FETTLING
Once the metal has solidified and cooled it is taken into the fettling shop and allowed to cool completely. Fettling involves knocking the shell off, cutting off the cup, runners and risers (these are cleaned and recycled), removing the metal pins and core mix inside the bronze and then sand blasting the surface.
This is a point where artists can take their sculptures away with them.
METAL WORK /CHASING
Particularly for larger pieces the bronze or bronze pieces need to be welded together and ‘chased’. Chasing is the term used for working the metal with a variety of hand and power tools to disguise the welding and replicate the artists marks and/or texture.
It is always our aim to reproduce the artists original in bronze as faithfully as possible.


PATINA & FINISHES
The artist is invited back to Talos when the bronze is finished and ready for its patination. They can also bring in their clients to watch and be involved in deciding the patination if it is there colour choice.
Applying a patina is done with heat and chemicals that are brushed/stippled onto the surface of the bronze and are then sealed with wax or lacquer, or both depending on their location.
Once coloured and cooled down, the artist can take the bronze away on the same day.
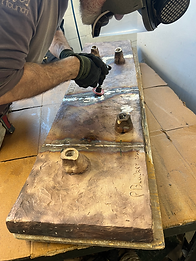
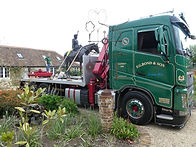
MOUNTING
Ordering bases made of slate or wood.
Drilling bases and mounting bronze on to them
INSTALLATION & SHIPPING
Transportation and installation of bigger commissions using our partners such as Seabird and FG Bond.
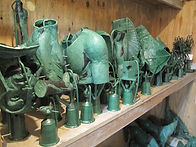
EDITIONS
If you have a mould already stored with us and are looking for further additions OR you have a mould already and are looking to have it recast. The process is as above and we will help you to recreate the same as the original or adapt accordingly.
special commissions
The sculpture, cast here in bronze at our Talos Art Foundry is the second edition by sculptor Caroline Wallace. Commissioned to mark Queen Elizabeth’s Platinum Jubilee the original stands outside the Royal Military Academy at Sandhurst.
The statue depicts The Queen mounted on her favourite charger, Burmese and is modelled on Her Majesty at Trooping the Colour in 1984. The mare Burmese was given to The Queen by the Royal Canadian Mounted Police in 1969 and was ridden by her at Trooping the Colour for 18 consecutive years.
Foundry and Gallery owner Richard Atkinson-Willes oversaw production and installation of the first edition at Sandhurst, where the sculpture was unveiled by Prince Edward.
Now riding high at our Talos Art Gallery & Gardens we offer the unique opportunity to get up close to this work — our Gallery in Wiltshire is open for a Summer Exhibition from 1 June to 27 July 2025.

